Implement ISO 9001 on Your Own: Is it Possible?
Implementing ISO 9001 might seem like scaling Mount Everest without a Sherpa—daunting and potentially risky. However, you can navigate this journey independently with the proper knowledge and tools. This saves substantial consulting fees and gives you complete control over your certification process. Self-implementation is possible and a path to your organization's long-term success.
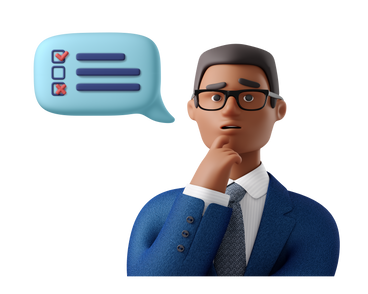
Evaluating the Need for a Consultant
Deciding between hiring an ISO 9000 consultant and implementing ISO 9001 independently requires careful consideration of your organization's capabilities and resources. While consulting ISO 9001 services can provide valuable expertise, they often come with significant costs that might strain your budget unnecessarily.
According to industry research, hiring a consultant can be a double-edged sword. While it may expedite the certification process, it can reduce employee engagement and limited understanding of QMS processes among top management. This disconnect could hamper the long-term effectiveness of your quality management system.
When evaluating whether to proceed without a consultant, consider these critical factors:
- Internal expertise and resources
- Available time for implementation
- Budget constraints
- Industry complexity
- Staff capability and commitment
- Previous quality management experience
Your organization's size and complexity play crucial roles in this decision. Smaller organizations with straightforward processes might find it easier to implement ISO 9001 independently, while larger corporations with complex operations could benefit from professional guidance. However, this isn't a hard rule—small companies struggle without guidance, and large organizations succeed independently.
The key advantage of implementing ISO 9001 without a consultant lies in developing deep internal knowledge and ownership of your QMS (quality management system). When your team directly engages with the implementation process, they gain a thorough understanding of the standard's requirements and how they apply to your specific operations.
Consider this: consultants can provide valuable shortcuts and prevent common mistakes, but they might also create dependency. By taking the independent route, you can maintain complete control over whatever quality management system you implement and make necessary adjustments without external support.
Choosing not to hire a consultant doesn't mean you're alone. Resources, training materials, and support networks are available to guide you through the implementation process. The key is to assess your organization's readiness honestly and make an informed decision based on your circumstances.
Could AI help you implement iso 9001?
Artificial Intelligence has revolutionized numerous business processes, including ISO 9001. This should fill you with optimism about the future of your quality management system.
AI can assist in several crucial aspects of ISO 9001 implementation by automating documentation processes, monitoring compliance, and identifying potential areas of improvement. Through machine learning algorithms, AI systems can detect patterns/anomalies that might be missed during manual reviews.
Key areas where AI can support your ISO 9001 implementation include:
- Document management and version control
- Risk assessment and analysis
- Process monitoring and measurement
- Corrective action tracking
- Internal audit preparation
- Performance trend analysis
One significant advantage of using AI during implementation is its consistency across all quality management processes. Unlike human operators, AI systems (generally) apply rules consistently, reducing the likelihood of inconsistencies in your quality management system.
AI-powered tools can also help predict potential non-conformities before they occur, allowing organizations to take preventive actions proactively. This predictive capability aligns perfectly with ISO 9001's emphasis on risk-based thinking and continuous improvement.
However, it's important to note that AI should be viewed as a supportive tool rather than a complete replacement for human oversight. While AI can handle routine tasks and data analysis, human judgment remains king regarding strategic decisions and interpreting complex situations that require context and experience.
Integrating AI into ISO 9001 implementation represents a significant step forward in modernizing quality management systems. By leveraging AI capabilities, organizations can achieve more accurate, efficient, and sustainable implementation while maintaining the human element necessary for successful quality management.
AI chatbots for ISO 9001
AI chatbots offer instant support and guidance for ISO 9001 implementation. Digital assistants provide round-the-clock support, ensuring consistent information delivery across your organization.
Botable is a specialized AI chatbot explicitly designed to meet quality assurance needs. Advanced AI technology helps to answer employee questions about SOPs, Work Instructions, and various quality documents, eliminating the traditional delays in accessing critical information.
AI chatbots in ISO 9001 systems offer several key advantages:
- 24/7 availability for instant query resolution
- Consistent interpretation of quality procedures
- Reduced burden on quality management teams
- Improved employee engagement with quality processes
- Real-time access to documented information
- Tracking of frequently asked questions for process improvement
One of the most significant benefits of using a platform like Botable is its ability to centralize all quality-related communications. This centralization allows quality assurance teams to identify common pain points, track understanding gaps, and make data-driven process improvements.
Employees with questions about quality procedures or ISO 9001 requirements can instantly connect with the AI chatbot instead of waiting for human assistance. Immediate access to information improves compliance with quality standards.
The system's ability to learn from interactions means it becomes more sophisticated over time, adapting to your organization's specific needs and terminology. As employees interact with the chatbot, it builds a comprehensive knowledge base that reflects your unique quality management system (QMS).
Quality managers can use the insights gathered through chatbot interactions to identify areas where additional training or documentation might be needed.
{{cta}}
Introduction to ISO 9001 Certification
ISO 9001 quality management standards represent the global gold standard for organizational excellence. They serve as a framework that over a million organizations rely on to deliver consistent quality. As a certified quality management system, ISO 9001 provides a structured approach to meeting customer expectations while fostering continuous organizational improvement.
At its core, ISO 9001 operates on seven fundamental principles:
- customer focus
- leadership
- engagement of people
- process approach
- improvement
- evidence-based decision-making
- relationship management.
These principles form the backbone of any successful quality management system certification ISO 9001 implementation, regardless of whether you work with a consultant or go solo.
The 2015 version of the standard (ISO 9001:2015 quality management system) introduced significant changes, including a stronger emphasis on risk-based thinking and leadership engagement. This made the standard more flexible and adaptable to various organizations, making it more feasible for companies to implement without external consultation.
The beauty of ISO 9001 lies in its adaptability. It's not a rigid set of rules but a versatile framework that can be tailored to your organization's unique needs. The ISO 9001-certified quality management system can be customized to enhance operational efficiency and customer satisfaction. This adaptability should reassure you that you're choosing to implement ISO 9001 independently.
Key components of ISO 9001 include:
- Documentation of processes and procedures
- Regular internal audits
- Management review meetings
- Continuous improvement initiatives
- Risk and opportunity assessment
- Customer satisfaction monitoring
Step-by-Step Guide
Implementing ISO 9001 without a consultant requires care. Here are some manageable steps to guide you through your certification journey effectively.
Step 1: Gain an understanding of ISO 9001
- Obtain and study the official ISO 9001 standard.
- Familiarize yourself with key terminology and concepts
- Identify the requirements relevant to your organization
- Research successful implementation examples in your industry
Step 2: Gap Analysis
- Evaluate your current processes against ISO requirements
- Document existing quality practices
- Identify areas needing improvement
- Create a detailed action plan addressing gaps
Step 3: Developing Documentation
- Create your quality policy
- Establish quality objectives
- Document mandatory procedures
- Develop required process documentation
- Set up record-keeping systems
Step 4: Building Your Quality Management System
- Design processes that align with ISO requirements
- Establish performance metrics
- Create monitoring and measurement systems
- Develop risk management procedures
- Set up internal communication channels
Step 5: Training and Implementation
- Train employees on new procedures
- Assign roles and responsibilities
- Establish internal audit programs
- Create corrective action processes
- Monitor implementation progress
Step 6: Internal Audit and Review
- Conduct comprehensive internal audits
- Review audit findings
- Implement necessary corrections
- Document improvements
- Prepare for certification audit
Each step in this process requires planning and execution of the QMS. The key to successful implementation is maintaining consistent progress while ensuring thorough understanding and adoption at each stage.
Focus on engaging your team throughout the process, as their buy-in and understanding are crucial for long-term success. Regular communication and feedback sessions help identify potential issues early and ensure smooth implementation across all departments.
Implementation
With the right approach, becoming compliant is entirely achievable without external consultation. Research shows that organizations taking this route often develop a deeper understanding of their quality management system, leading to more sustainable long-term results.
Building iso 9001 experience internally starts with strong leadership commitment. According to industry experts, full support and involvement from top management are crucial for successful implementation. This commitment should be visible through active participation in quality initiatives and resource allocation for the implementation process.
Key implementation strategies include:
- Utilizing pre-designed templates and procedures
- Developing comprehensive documentation
- Establishing clear communication channels
- Creating effective training programs
- Setting up monitoring mechanisms
- Implementing feedback systems
Studies indicate that while implementing ISO 9001 without a consultant can be time-consuming, pre-designed quality manuals and procedures can significantly streamline the process. These resources provide a solid foundation while allowing customization to meet your organization's needs.
Documentation is another critical aspect of implementation. Industry data suggests that organizations should focus on creating clear, accessible documentation that serves practical purposes rather than just meeting certification requirements. This approach helps ensure that quality processes become integrated into daily operations rather than existing as separate procedures.
Internal audits are essential for maintaining system effectiveness. According to implementation experts, establishing a robust internal audit program helps identify areas for improvement early and ensures continuous compliance with ISO 9001 requirements.
Remember that the implementation process is iterative. Studies show that organizations that approach implementation as a continuous improvement journey rather than a one-time project achieve better long-term results. This mindset helps create a more resilient and adaptable quality management system.
Key success factors include:
- Strong leadership commitment from the start
- Employee involvement in process development
- Clear communication channels
- Practical and straightforward documentation
- Regular internal training sessions
- Effective use of available resources
- Continuous monitoring and improvement
Successful organizations emphasize the importance of making the quality management system work for their specific needs rather than forcing their operations to fit a generic template. This approach resulted in more sustainable and effective quality management systems.
The success stories highlight how independent implementation often leads to deeper organizational understanding and ownership of quality processes. Many reported that the journey took longer without a consultant, but the resulting system was more robust and better integrated into their daily operations.
Answers your employees need, right when they need them
Meet Botable — the AI chatbot that handles everything from simple FAQs to complex, multi-step questions, so your team can focus on what matters. Built for HR, QA, and beyond.
Continue reading
Ready to see what Botable can do for you?
Book your demo now to see how Botable can transform your workplace.
Identify your unique challenges
Flexible pricing options
Easy integrations
Step-by-step implementation plan
Customize Botable for your workflow
Book a demo
.webp)